FASAN
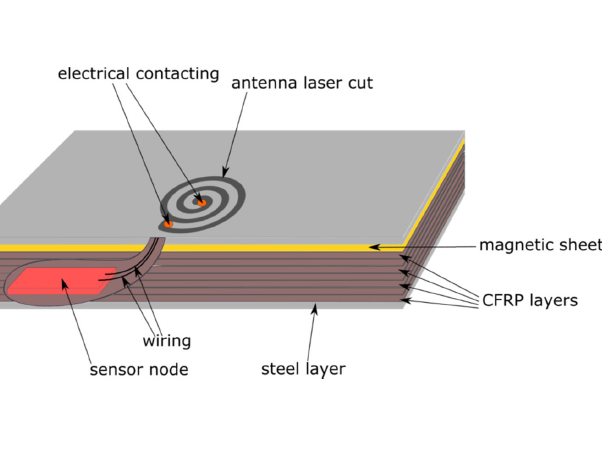
Subject of the IMSAS project „FASAN“ is the wireless power provision for newly developed sensors for structural health monitoring (SHM) in fiber-in-metal-laminates (FML), as well as wireless data acquisition of those sensors.
Thematic Embedment
Fibre Composites are already in use in various fields due to the benefits they offer. Fibre-metal-laminates (FML), built of alternating layers of fibre composites and metal foils combine benefits of both materials while optimizing drawbacks. One area profiting from the lightweight characteristics of FMLs with simultaneously high geometrical stability is the aerospace industry. FML technology is getting more and more used in recent production of aircraft parts. Examples are the fuselage and tail unit of the Airbus A380.
Low velocity impacts like bird strikes, hail, debris on the runway or similar objects can lead to hidden damages in the FML which can result in delamination of layers under mechanical stress. Since these delaminations cannot be detected just by visual inspection, complex procedures for the inspection of FML parts are needed resulting in longer maintenance times and higher operating costs. To reduce the planes’ down-time an integration of wireless sensor networks into the FML structures can lead to an easier detection of damages. With integrated sensors it will be possible to get quick information about the state of health of the airplane parts during normal inspection times.
Project Description
Within the scope of the research unit FOR3022 founded by the DFG, a wireless state-of-health monitoring for fibre-metal-laminate components via lamb-waves shall be developed. For this purpose, scientists of TU Braunschweig, University of Bremen and Helmut Schmidt University of Hamburg, with participation of the German Aerospace Center (DLR) are working together.
In the subproject “FASAN“ a wireless connection to and a power provision for a newly developed sensor for SHM in FMLs will be realized. An antenna structure will be designed with which energy is transmitted to the sensor. The Data picked up by the sensor is then transmitted to a reading unit for evaluation. The working approach of this novel antenna is the structuring of the outer metal layer of the FML into a proper antenna structure. Possible problems might occur because of the fibre’s conductivity in the inner layer of the FML. Another point to be aware of is the change of the FML´s material Integrity due to the integration of sensors in said material. Despite integration of both the sensor and the needed electronic components for connection, structural changes need to be kept to a minimum.
Project Partners
Privat-Dozent Dr. rer. nat. Stefan Bosse
Universität Bremen, Fachbereich3: Mathematik und Informatik
Prof.Dr. rer. nat. Andreas Dietzel
TU Braunschweig, Institut für Mikrotechnik
Dr.-Ing.. Axel von Hehl
Leibniz-Institut für Werkstofforientierte Technologien IWT
Prof.. Dr.-Ing. Axel S. Herrmann
Faserinstitut Bremen e. V. (FIBRE)
Prof.Dr.-Ing. Christian Hühne
TU Braunschweig, Institut für Adaptronik und Funktionsintegration
Prof.. Dr.-Ing. Rolf Lammering
Helmut-Schmidt-Universität Hamburg, Fakultät für Maschinenbau
Prof.. Dr. rer. nat. Dirk Lorenz
TU Braunschweig, Carl-Friedrich-Gauß-Fakultät, Institut für Analysis und Algebra
Dr.-Ing. Steffen Opitz
Deutsches Zentrum für Luft- und Raumfahrt e. V., Institut für Faserverbundleichtbau und Adaptronik
Dr.-Ing. Natalie Rauter
Helmut-Schmidt-Universität Hamburg, Fakultät für Maschinenbau
Dr.-Ing. Daniel Schmidt
Deutsches Zentrum für Luft- und Raumfahrt e. V., Institut für Faserverbundleichtbau und Adaptronik
Prof.. Dr.-Ing. Michael Sinapius
TU Braunschweig, Institut für Adaptronik und Funktionsintegration
Dr.-Ing. habil. Wolfgang Weber
Helmut-Schmidt-Universität Hamburg, Fakultät für Maschinenbau
Contact
M.Sc Sarah Bornemann
Universität Bremen
Phone: +49 421 218 62645
E-mail: contact
Prof.. Dr.-Ing. Walter Lang
E-mail: contact
The project is funded by the DFG - Deutsche Forschungsgemeinschaft from 2020 onwards for 6 years, projectnumber 418311604. Spokesperson of the research group is Professor Michael Sinapius, Institut für Adaptronik und Funktionsintegration of Technical University, Braunschweig.